Our Ukrainian partner Materials Research Centre(MRC) offers manufacturing of Etching Reactor for MXene synthesis.
Our partners from MRC (Kiev, Ukraine) design and manufacture laboratory reactors for stable MXene synthesis with controlled synthesis parameters, that allows to obtain up to relatively big quantity of MXene per batch ( up to 20-100g). Even relatively exotic MXenes can be manufactured in tens of grams per batch in laboratory environments, which is already a large amount for any nanomaterial. The ability to scale up MXene synthesis allows for rapid testing in a variety of fields, where large quantities are needed. Synthesis of even 50–100 g batches of MXene provides the opportunity for commercial production of, for example, MXene inks for printing electronic devices and many others.
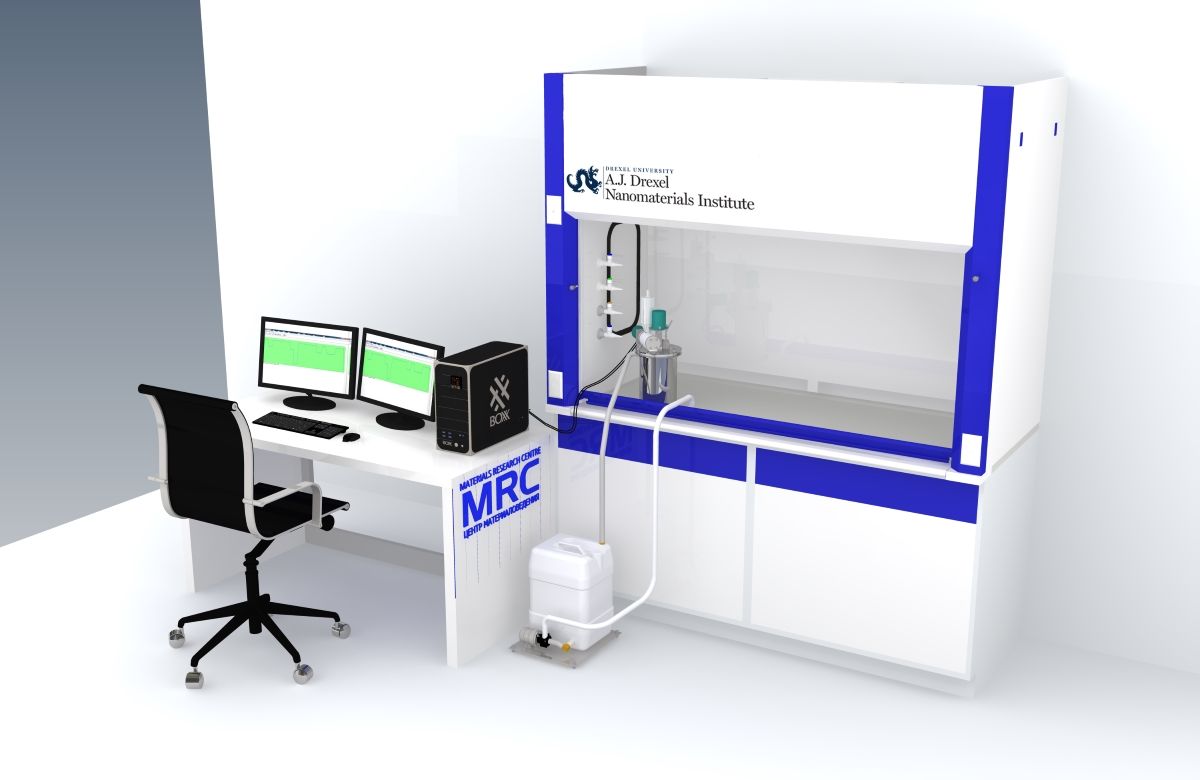
MRC mission is technology development, design and manufacturing of specialized laboratory equipment for different research needs. Our staff includes engineers trained in design, manufacturing, as well as nanotechnology, chemistry, electrochemistry, and materials science. We can help you to develop solutions for your needs within a wide range of materials and equipment for their manufacturing.
ETCHING REACTOR FOR ACID ETCHING OF MAX-PHASE POWDERS, PRODUCTIVITY UP to 100 g / DAY
While most nanomaterials are only available in “nano” quantities, research team of professor Yury Gogotsi in Drexel Nanomaterials Institute, Drexel Universuty (USA) can make in their lab as much as 100 grams of MXene at a time, using a reactor developed with the Materials Research Center in Ukraine.
The reactor with controlled feed rate and temperature allows rapid optimization of processing for your specific needs, and our engineering and sales team is always available to answer your questions.
Etching reactor with computer control system has the following advantages:
- automatically controlled cooling system for keeping stable temperature
- additional computer recording and displaying the temperature curves of the etching process
- computer control system for adjusting the rate of material feeding and mixing
- possibility to connect the supply of neutral gases through the process
- possibility to connect two monitors for operating and displaying of process parameters
- possibility to connect the control unit to laboratory/institutional computer network, monitor and operate the process parameters though intranet/internet remote computer access
Operation
Solution for MAX-phase for etching is poured into reactor and hermetically closed by a cover, which enables a controlled and safe removal of hydrogen.
MAX-phase feeding is done at a constant rate. To prevent deposition of material, the solution is constantly mixed. Chemical reaction of MAX-phase etching is exothermic. A water-cooled shell and feeder for material supply are designed for the temperature control.
MAX-phase etching is done following, for example, the reaction:
Ti3AlC2 + 3HF + 2H2O = AlF3 + 5/2H2 + Ti3C2(ОН)2
Hydrogen that is formed during the etching process flows into the discharge system for further utilization or is discharged. After etching, the solution is discharged for product purification from reaction products and other impurities.
Read more about the MXene synthesis technology in our publication:
C. E. Shuck, A. Sarycheva, M. Anayee, A. Levitt, Y. Zhu, S. Uzun, V. Balitskiy, V. Zahorodna, O. Gogotsi, and Y. Gogotsi, Scalable Synthesis of Ti3C2Tx MXene. Advanced Engineering Materials 22, 1901241(2020) https://doi.org/10.1002/adem.201901241
Publications about scaling up of MXene synthesis and Etching reactors:
Michel W. Barsoum, Yury Gogotsi, Removing roadblocks and opening new opportunities for MXenes, Ceramics International,Volume 49, Issue 14, Part B, 2023, Pages 24112-24122. DOI: 10.1016/j.ceramint.2022.10.051.
C. E. Shuck, A. Sarycheva, M. Anayee, A. Levitt, Y. Zhu, S. Uzun, V. Balitskiy, V. Zahorodna, O. Gogotsi, and Y. Gogotsi, Scalable Synthesis of Ti3C2Tx MXene. Advanced Engineering Materials 22, 1901241(2020) doi: 10.1002/adem.201901241
M. Alhabeb, K. Maleski, B. Anasori, P. Lelyukh, L. Clark, S. Sin, Y. Gogotsi, Guidelines for Synthesis and Processing of 2D Titanium Carbide (Ti3C2Tx MXene), Chemistry of Materials, 2017, 29 (18) 7633-76445.
Hossein Riazi, Srinivasa Kartik Nemani, Michael C. Grady, Babak Anasori, Masoud Soroush, Ti3C2 MXene–polymer nanocomposites and their applications, J. Mater. Chem. A, 2021,9, 8051-8098. doi: 10.1039/D0TA08023C
C. E. Shuck and Y. Gogotsi, “Taking MXenes from the Lab to Commercial Products” Chemical Engineering Journal, vol. 401, pp. 125786, 2020
Pritishma Lakhe, Safety in Process Scale-up of MXene and Graphite Oxide Production, PhD Thesis, Texas A&M University, 2020
Fundamental Aspects and Perspectives of MXenes, Editors: Mohammad Khalid, Andrews Nirmala Grace, Arunachalam Arulraj, Arshid Numan. Series Engineering Materials, Springer International Publishing, 2022
Chao Peng, Tao Zhou, Ping Wei, et al. Photocatalysis over MXene-based hybrids: Synthesis, surface chemistry, and interfacial charge kinetics. APL Mater. 9, 070703 (2021); doi: 10.1063/5.0055711
MRC and Carbon-Ukraine offer MXene technology development, Flexible engineering design, Customized manufacturing tailored to meet your needs
MRC encourage you to learn more about the exciting possibilities we can offer you, and we look forward to partnering with you to improve your material's synthesis and manufacturing.
To buy high quality MXenes or MAX phases from reliable MXene supplier for research needs and for further information and detailes about ordering Etching Reactor for MXene synthesis please contact us at This email address is being protected from spambots. You need JavaScript enabled to view it.
or our partners at This email address is being protected from spambots. You need JavaScript enabled to view it.
To get a quota with price on MXene synthesis or price on MAX phase powders please contact us at This email address is being protected from spambots. You need JavaScript enabled to view it.